タイに生産拠点を持つ日系製造企業では、現場管理において様々な課題に直面しがちです。
例えば、
「現場の遅れがなかなか改善されない」
「帳票が紙のままで非効率になっている」
「タイ人スタッフへの教育が属人的で標準化できない」
といった悩みに心当たりはありませんでしょうか。
この記事では、そうしたタイ現地の生産管理にありがちな課題を整理し、共感できるポイントと共に現実的な改善ステップを解説します。
さらに、タイの現場で成功した改善事例や、日系企業向けに現地サポートを行うTOMAS TECHの支援内容についても紹介します。タイでの生産管理改善のヒントをぜひ参考にしてみてください。
タイ現地での生産管理にありがちな課題とは?
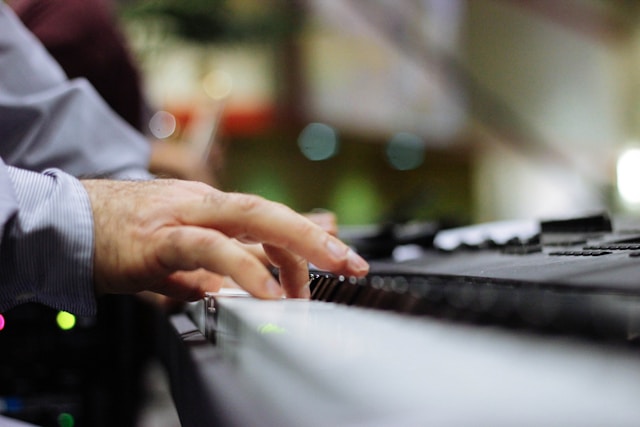
日本とは異なる文化・習慣の中で工場運営を行うタイでは、生産管理上のよくある課題が存在します。ここでは、タイ現地の製造現場でありがちな3つの課題について見ていきましょう。
計画通りに生産が進まない
タイの生産現場では、生産スケジュールの遅れが発生しても原因究明や再発防止が進まず、同じ遅延が繰り返されるケースが少なくありません。例えば部品納品の遅れやライン停止が起きても、紙の報告書や口頭連絡に頼っていては現場状況の把握に時間がかかり、対策が後手に回ってしまいます。
また、日本人駐在者が遠隔で複数の現場を管理している場合、進捗をリアルタイムに把握しづらいことも遅れ改善を妨げる一因です。
現場の状況を見える化して遅延箇所や原因を把握することが必要ですが、属人的な管理や紙ベースの情報では全体像が掴みにくく、効果的な改善策を立てづらいのが現状です。
在庫や進捗がリアルタイムで把握できない
タイの工場では、生産現場の帳票(日報・検査記録・在庫表など)を紙で運用しているケースが多く見られます。紙の帳票は記入や回覧に時間がかかり、情報共有のタイムラグが発生しやすいです。
例えば、現場で記録した生産数量や不良情報を後から担当者がExcelに再入力するなど、無駄な手間が日常的に発生する可能性も。このような紙からデータへの転記作業はヒューマンエラー(入力ミス)も招きやすく、データの精度や活用に支障をきたします。
また、紙書類は過去情報の検索にも時間がかかり、現場全体のスピード感を損なう原因となっています。
属人的な管理が多く、教育が引き継げない
生産管理における現地スタッフの教育にも課題があります。育成方法が特定の人の経験や勘に頼った属人的なものになりがちで、標準化された教育マニュアルや仕組みが整っていないことが多いのです。
例えば、日本人上司やベテランのタイ人がマンツーマンのOJT(現場訓練)で指導し、その人の教え方次第で新人の習熟度が大きく変わってしまう、といった状況です。
このように教育が属人化していると、担当者が異動・退職するたびにノウハウがリセットされてしまいます。実際、タイでは従業員の転職(ジョブホッピング)も珍しくなく、せっかく育てた人材が流出してしまうという声も聞かれます。
教育資料が整備されず口頭での引き継ぎに頼る状態では、いつまで経っても「人に依存しない仕組み」が築けず、管理レベルが安定せず悪循環に陥ります。
これらの課題は多くの日系企業が直面しています。まず自社の問題点を正しく認識することが改善への第一歩です。もし少しでも思い当たる節があるなら、早めに専門家に相談して現状を客観的に分析してもらうのも有効でしょう。課題解決のプロに相談してみませんか?
タイの生産管理の改善に必要な3つのステップ
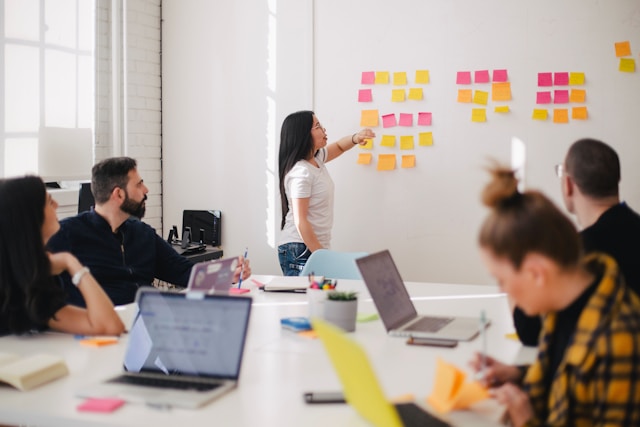
上で挙げた課題を解決し、タイでの生産管理を改善するには、闇雲に対策を講じるのではなく段階を踏んだ計画的なアプローチが重要です。ここでは、現地で効果的に改善を進めるための3つのステップを紹介します。
現場の課題を「可視化」する
まず取り組むべきは、現地要件の整理です。タイの工場ならではの事情や制約、そして現場の真のニーズを洗い出します。日本本社の理想を押し付けるのではなく、現地経営者から作業員までヒアリングし、どこに問題が潜んでいるかを可視化しましょう。
日本人とタイ人の間のギャップを埋めるため、必要に応じて通訳や現地コンサルタントの協力を得て現場の声を正確に吸い上げることもポイントです。現状課題が明確になれば、次に何から改善すべきかの道筋が立てやすくなります。
簡単なITツールから導入を始める
次に、解決策を段階的に導入していきます。一度にすべてを変えようと大規模改革を行うと現場が混乱し抵抗も大きいので、スモールスタートで着実に進めることがポイントです。例えば、まず紙の帳票をタブレット入力に切り替えるなど、小さなデジタル化から始めます。日報を電子化するだけでも情報共有のスピードが上がり効果を実感できるでしょう。
その後、データが蓄積できたら生産計画や在庫管理へと順にDX(デジタルトランスフォーメーション)を拡大していきます。段階的に進めれば現場スタッフも新しい仕組みに慣れやすく、トラブルが起きても影響を小さく抑えられます。「急がば回れ」の精神で一歩ずつ進めることが成功への近道です。
全体最適のシステム化を目指す
最後に、各工程間の情報連携を強化して全体最適を図ります。生産管理には調達・製造・物流・品質など多くの部門が絡むため、部分的な改善だけでは限界があります。各工程のデータを一元管理し、部門の壁を越えてリアルタイムに情報共有できる仕組みを作りましょう。例えば、生産スケジュールと部品在庫を連動させたり、工程間で進捗や問題点を即座に共有できるようシステムを統合します。
これにより工程間の伝達漏れが防止され、工場全体で協調して生産性を高めることが可能になります。また、経営層も統合ダッシュボードで全体状況を把握でき、迅速な意思決定に繋がります。工程連携とデータ一元化は見える化の完成形とも言え、ここまで達成できればタイの生産管理は飛躍的にレベルアップするでしょう。
タイの現場で生産管理が成功した改善事例
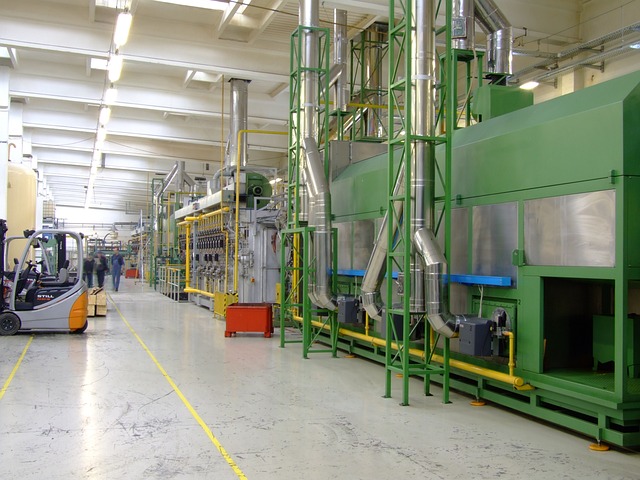
ある日系の自動車部品メーカーのタイ工場では、現場帳票の電子化によって生産管理の効率化に成功しました。同社では、生産数量や不良情報を紙の用紙に手書きし、その後担当者がExcelに再入力するというアナログな運用を続けており、手間とミスが多く情報共有にも時間がかかっていました。
そこで紙の帳票レイアウトをそのままタブレットで使える電子帳票システム「i-Reporter」を導入したところ、二度手間の解消と記入ミスの激減を実現しました。現場で入力されたデータはリアルタイムにクラウドへ集約されるため、管理者や日本本社も即座に状況を把握できるようになり、報告のタイムラグが解消されました。
情報伝達の迅速化とデータ精度向上によって現場の対応スピードが大幅に向上し、遅延やムダの削減につながっています。
タイで生産管理をするためにTOMAS TECHが支援できること
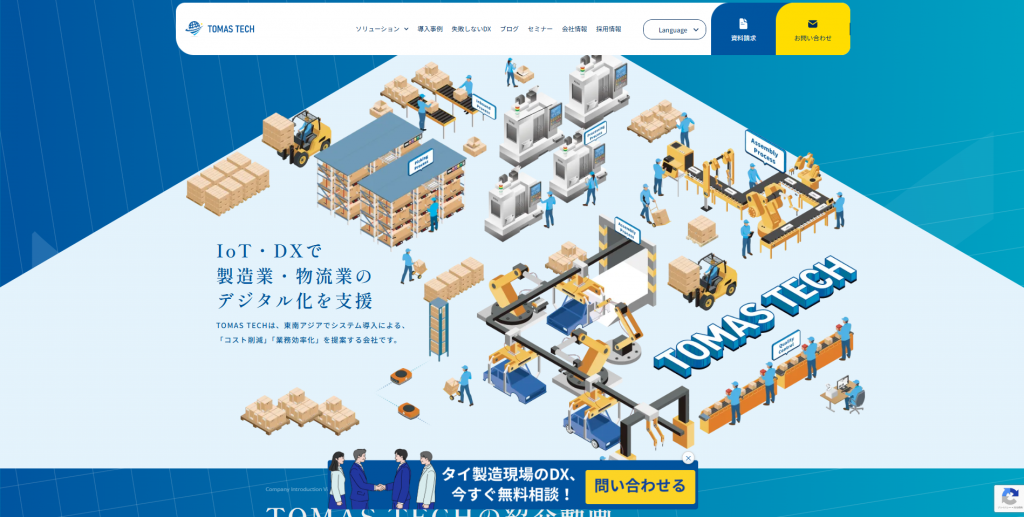
タイでの生産管理の改善には、現地事情に通じたプロの支援を活用するのも有効です。例えばTOMAS TECHは、タイに拠点を置き製造業の生産管理や在庫管理のDXを支援している頼れるパートナーです。日本企業の課題に寄り添いながら現地導入をトータルにサポートしており、主に次のような内容で支援しています。
- 現地要件の整理支援:多言語対応のスタッフが現場をヒアリングし、タイ現地の業務要件や課題を洗い出して明確化します。
- 段階的な導入支援:小さく始めて順次拡大する導入計画を立て、各段階で現場への定着まで丁寧にサポートします。
- 工程間のシステム連携:生産管理システムと在庫・物流システムを連携させ、全社でリアルタイムに情報共有できる環境を構築します。
これらをワンストップで提供できるのがTOMAS TECHの強みです。現地スタッフへの多言語トレーニングや導入後のフォロー体制も整っており、初めてタイでシステム導入する企業でも安心です。
「現地に詳しいパートナーの力を借りて生産管理を改善したい」という場合は、TOMAS TECHに相談してみてはいかがでしょうか。専門家が課題を整理し、御社の状況に合ったプランを提案してくれます。サービスの詳細はこちら。
タイの生産管理に関するよくある質問
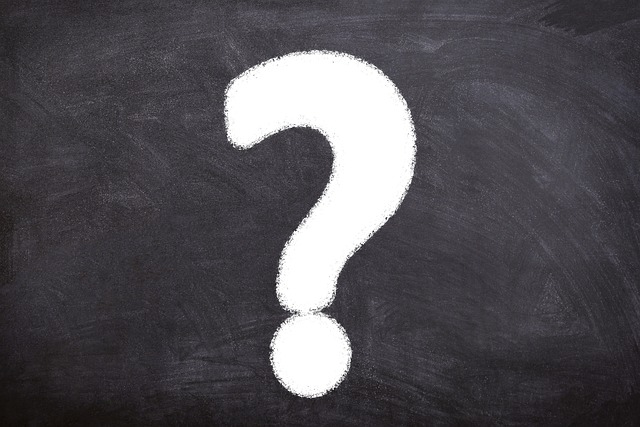
ここからは、タイの生産管理に関するよくある質問に回答していきます。
はい、可能です。まずは「紙やExcelをやめる」「現場の入力端末を導入する」など、一部の工程から小さく始める方法がおすすめです。現場の混乱を防ぎながら、徐々に範囲を広げていくことができます。
現場での運用を想定した多言語対応のUIや操作マニュアル整備が重要です。
TOMAS TECHでは、日本側とタイ側の両言語対応サポート体制を用意しており、教育やトレーニング支援も可能です。
工場規模や導入範囲によって異なりますが、月額課金型の簡易ツールから、自社専用のフルカスタム型まで幅広い選択肢があります。
まずは予算と課題に応じたプランを提案する「ヒアリング+簡易診断」から始めてみてください。
まとめ:タイでの生産管理は「段階的な可視化」が鍵
タイの生産現場でありがちな課題と、その改善の進め方について解説してきました。「現場の遅れ」「紙の非効率」「教育の属人化」といった問題も、適切な手順を踏めば改善できます。その際のポイントが、段階的に現場を可視化していく取り組みです。
一度に完璧を目指すのではなく、一歩ずつデータを集めて見える化し、課題を浮き彫りにしながら解決策を講じていくことで現場は着実に変わっていきます。 タイでの生産管理は決して日本と同じやり方では進みませんが、現地の実情に合わせた正しいアプローチを取れば道は開けます。
もし自社だけでの対応に限界を感じたら、現地支援のプロの力を借りてみましょう。パートナーと協力すれば、解決までのスピードと確実性は格段に増します。生産管理改善のプロに相談して、次の一手を踏み出してみませんか?